Business as Usual (BAU) represents standard operating procedures and time-tested practices that are the foundations of an organization’s daily operations. BAU covers routine activities in departments of all sizes, such as production, sales, marketing, finance, and administration that keep operations stable.
Project-based work has defined endpoints, but BAU activities continue indefinitely and keep systems stable and secure. These activities include processing customer transactions, managing inventory, handling accounting functions, and providing regular maintenance. Organizations use BAU as a baseline to review changes, state-of-the-art solutions, and strategic initiatives.
BAU’s importance goes beyond day-to-day operations. A well-laid-out BAU framework creates clear ownership, governance, support processes, and performance monitoring systems. Organizations can maintain strong operational assets that consistently deliver value through this structured approach. Proper BAU governance makes decision-making processes clear, defines roles, implements controls, and creates working practices to review operational performance.
The financial side of BAU operations offers ways to optimize costs after the original implementation investments. Organizations streamline their support staff levels and build efficient internal capabilities for maintenance, upgrades, and ongoing support. Notwithstanding that, BAU requires a delicate balance between operational efficiency and adaptability to tackle emerging challenges.
Technology implementations often overlook the transition to BAU state. Organizations risk lower adoption rates and training gaps that can hurt long-term success without proper transition planning. Building robust knowledge transfer processes, detailed documentation, and appropriate support models becomes crucial to sustain operational excellence.
BAU differs from projects or programs that bring change. While it represents the status quo of operations, effective BAU management needs constant monitoring, optimization, and adaptation to keep organizations resilient in dynamic business environments.
Business as Usual Framework
A well-laid-out BAU framework creates strong foundations to help organizations run smoothly. This framework includes three important parts that come together to ensure business operations run without interruption.
Core Components of BAU Operations
The life-blood of BAU operations comes from its repetitive nature that delivers consistency and keeps things stable. BAU operations include everyday tasks like system monitoring, backup management, and patch implementation. These operations use standard operational budgets instead of project-specific funding.
Key Stakeholders in BAU Management
The core team in BAU management consists of functional support teams, platform support specialists, and product owners. Here’s what each does:
- Product Owners: They work within business units to guide platform development and boost implementation returns
- Functional Support: They look after capability use, release management, and vendor relationships
- Platform Support: They handle technical configurations, integrations, and keep environments running
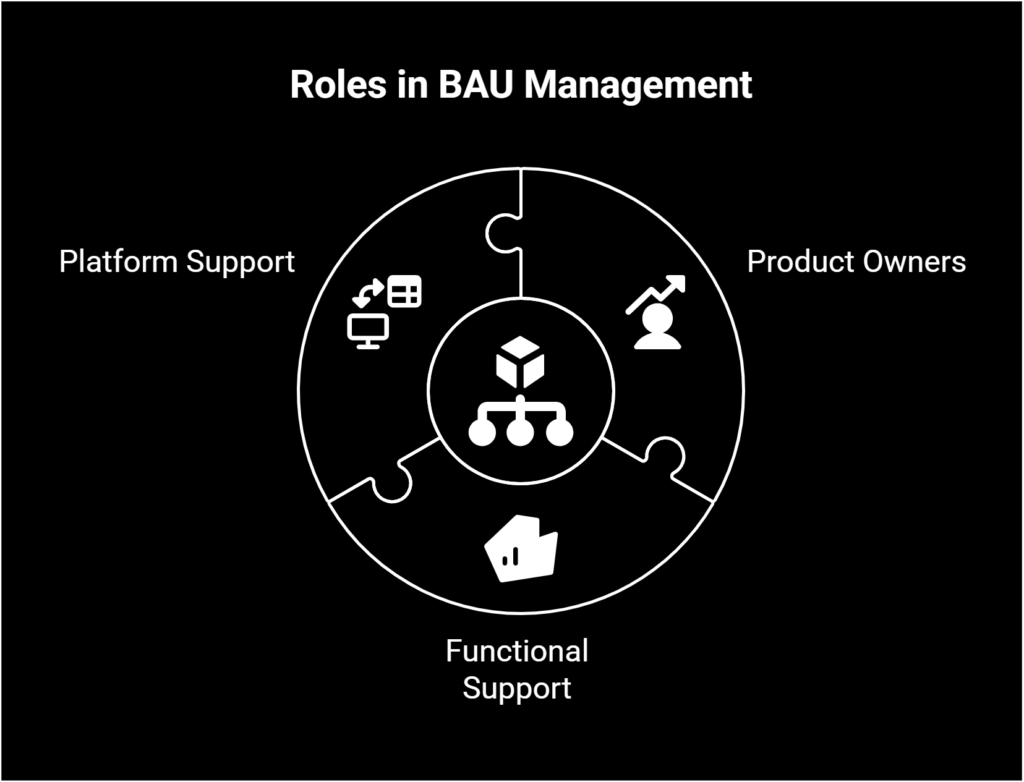
BAU vs Project-Based Work
The difference between BAU and project work shows up in several important ways. BAU spots changes that need to be made, while project teams put these changes in place. BAU teams focus on reducing risks and keeping the organization stable, so they take a more careful approach to change.
Here are the main differences:
- Time Horizon: BAU activities go on forever, while projects have clear start and end dates
- Risk Approach: BAU operations try to avoid risks, while projects actively manage them
- Team Structure: BAU has functional teams that work together regularly, unlike project teams that often bring new people together
- Change Impact: Projects bring organizational changes, while BAU makes existing processes better through small improvements
BAU operations aim to keep things consistent by making changes in small steps. BAU teams are usually the first to notice when existing processes need changes because they run daily operations. This insight helps identify improvements needed and keeps operations running at their best.
Measuring BAU Process Excellence
Performance metrics are the life-blood of successful BAU operations. Organizations can learn about areas to improve and maintain operational excellence through systematic measurement and analysis.
Everything in BAU Performance Metrics
We focused on maintaining baseline performance rather than strategic improvements in BAU metrics. The core metrics cover:
Process Performance Indicators:
- Production efficiency measured as production time per stage divided by total processing time
- Total cycle time tracking start-to-finish process duration
- Throughput calculations showing units produced per production time
- Error rates determining total errors versus total units produced
Operational Health Metrics:
- Resolution rates for support issues
- System availability tracking
- Process efficiency measurements
- Problem recurrence monitoring
Up-to-the-minute Monitoring Systems
Modern BAU operations just need reliable real-time monitoring capabilities that provide quick insights and rapid response. Advanced monitoring systems deliver:
Data Collection Features:
- Machine data collection that automatically delivers insights within minutes
- Ground machine diagnostics that enable condition-based maintenance
- Machine status visualization through color-coded dashboards
Performance Analysis Tools:
- Hour-by-hour utilization tracking across shifts, days, and weeks
- Automated incident tracking with full audit capabilities
- Pareto charts that highlight common inefficiency sources
Reporting Capabilities:
- Reports accessible via laptops, tablets, and phones
- Instant alerts that trigger immediate action on shop floor issues
- Seamless integration with existing ERP systems
BAU monitoring works when organizations ensure their metrics stay timely, detailed, accurate, and relevant. On top of that, teams should see performance data visually with clear indicators of under/over-performance to spot trends and make needed adjustments quickly. These metrics must provide useful insights that help teams maintain expected performance levels and spot opportunities to refine processes.
Implementing BAU Process Controls
Process controls are the life-blood of maintaining stable BAU operations. These controls help deliver consistent performance, reduce errors, and protect organizational assets through systematic oversight.
Standard Operating Procedures (SOPs)
SOPs are the foundations of process control that provide step-by-step instructions for routine activities. These documented guidelines spell out specific tasks and ensure consistency in operations. Good SOPs should be brief but complete, with clear focus on task execution. Companies should review and update these procedures every six to twelve months to stay relevant.
Quality Control Checkpoints
Quality inspections act as vital checkpoints throughout production. Quality engineers spot defects and fix issues before they reach customers – from pre-production to final inspections. These checkpoints help:
- Cut production costs
- Build brand reputation
- Keep customers happy
- Catch safety risks early
Risk Management Protocols
Risk management protocols need a proactive approach to spot and handle potential threats. The main components include:
- Creating risk registers to document identified risks
- Setting up controls for specific risks
- Putting mitigation strategies in place
- Checking and reviewing risk status regularly
Documentation Requirements
Complete documentation gives transparency and accountability in BAU operations. The essential documentation includes:
- Process Models: Detailed workflow diagrams that show control steps
- Control Descriptions: Details of control types, frequency, and who’s responsible
- Technical Resources: Records of tools and systems used
- Execution Records: Proof of control implementation through protocols or system logs
Process controls work best when automated where possible. This automation gives up-to-the-minute insights, better visibility into risks and controls, and makes testing procedures faster. Organizations must line up their control framework with business needs while keeping operations efficient.
Conclusion
Business as Usual means much more than daily operations – it serves as the foundation of lasting organizational success. BAU includes everything needed for daily activities that need strategic oversight and continuous improvement.
Successful organizations show distinct patterns in their BAU management. They build resilient frameworks with well-defined stakeholder roles and responsibilities. Their detailed performance metrics and up-to-the-minute monitoring systems drive results. Strong process controls through specific SOPs and quality checkpoints complete their approach.
Technology has become a game-changer in BAU optimization. Modern automation tools have reduced manual workload substantially. Digital workflows have changed traditional processes completely. Companies that use these solutions see major improvements in efficiency. Their automation projects typically pay off within 12 months.
The most effective BAU operations balance stability with state-of-the-art approaches. Daily operations need consistency, yet organizations must adapt their BAU processes to meet new challenges and opportunities. This flexibility combined with proper governance and performance tracking leads to lasting operational excellence.
Mastering BAU management demands dedication to operational stability and continuous improvement. Organizations can turn their BAU operations from basic maintenance into drivers of lasting business success. They achieve this through smart implementation of frameworks, metrics, controls, and technology solutions.
- Shopify Statistics 2025: Revenue, Merchants & Market Dominance Analysis - August 4, 2025
- Cursor Growth Strategy: From MIT Dorm to $500M ARR in 21 Months - July 21, 2025
- TikTok Statistics 2025: Users, Revenue & Market Impact Analysis - July 21, 2025